The 1st Precision Machining Technology and Application International Summit was held concurrently with the DeburringTec. The forum contains multiple topics, including the innovation and application forum of precision and ultra-precision surface finishing technology, medical device & implant surface treatment technology and application forum, automatic grinding and polishing technology forum, auto parts cleanliness control technology forum, aviation Parts precision machining technology and application forum, deburring & surface finishing technology innovation and development forum in vertical application, auto parts cleanliness control technology forum seven contents. Focus on the innovation and development of cutting-edge precision machining technology and its vertical application, and jointly promote the development and advancement of global surface precision machining technology.
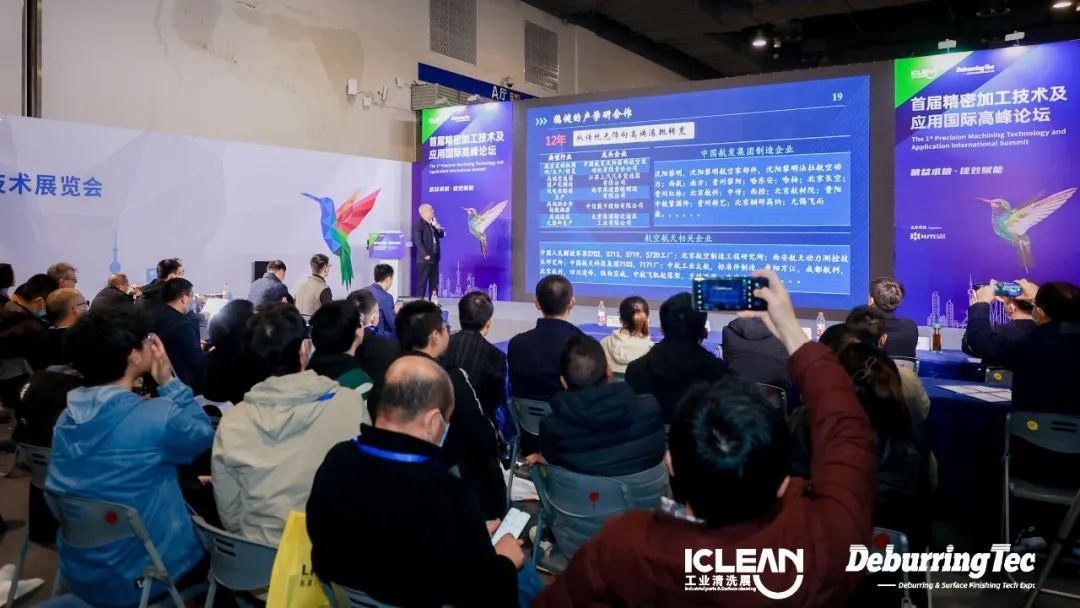
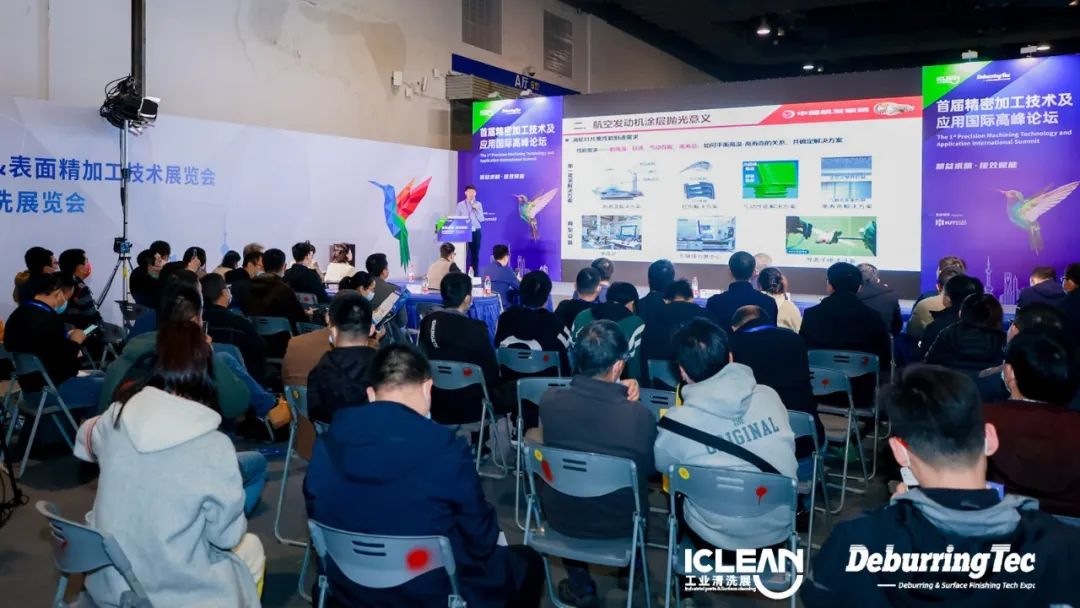
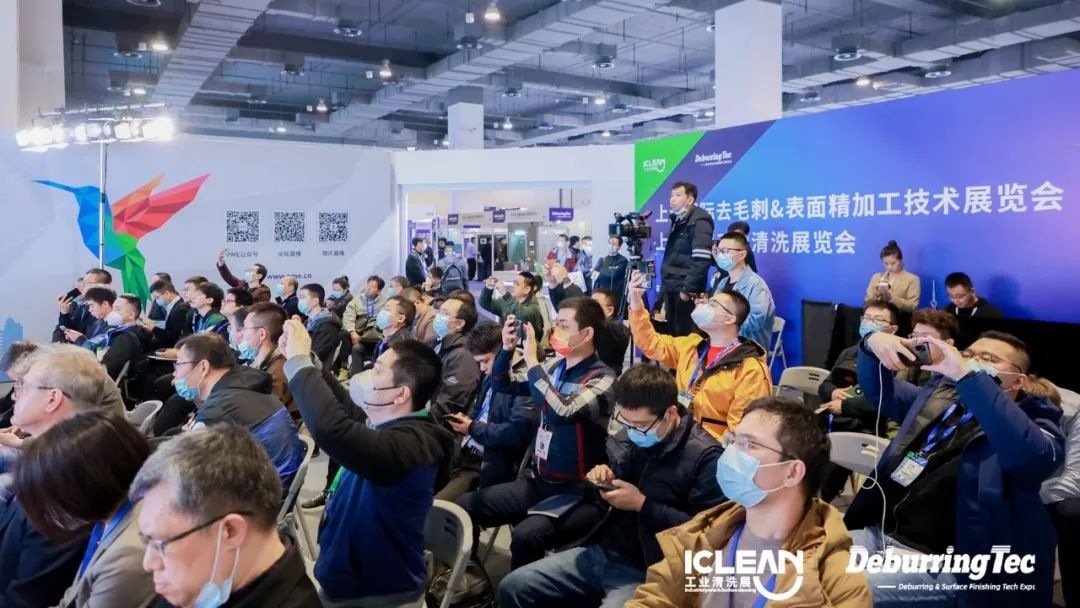

The theme of the forum on the morning of March 23 is: Precision Machining Technology and Application of Aviation Parts


Professor Xiao Guijian, College of Mechanical and Vehicle Engineering of Chongqing University, delivered a special speech on “Automatic Belt Grinding Technology and Application of Anti-Fatigue Surfaces”
Professor Xiao discussed four aspects: the background and significance of the research, the creation mechanism of surface integrity, the content of key technologies, and the promotion of engineering applications.
In terms of the application of intelligent bionic surface processing, Professor Xiao said that in recent years, my country has issued a series of documents on the development of circular economy, energy conservation and emission reduction, and green manufacturing, focusing on the reduction, Reuse, recycle, vigorously develop circular economy, focus on improving energy resource utilization efficiency and renewable resource utilization level, promote the realization of the strategic goal of “carbon peaking, carbon neutrality”, and emphasize the need to develop moderately economical, green and low-carbon living habits, Emphasize the comprehensive development of green manufacturing. The intelligent bionic surface has excellent environmental adaptability, and it can intelligently adapt to performance requirements due to environmental effects. How to expand production efficiency and enhance service life is crucial to the development of intelligent surfaces.
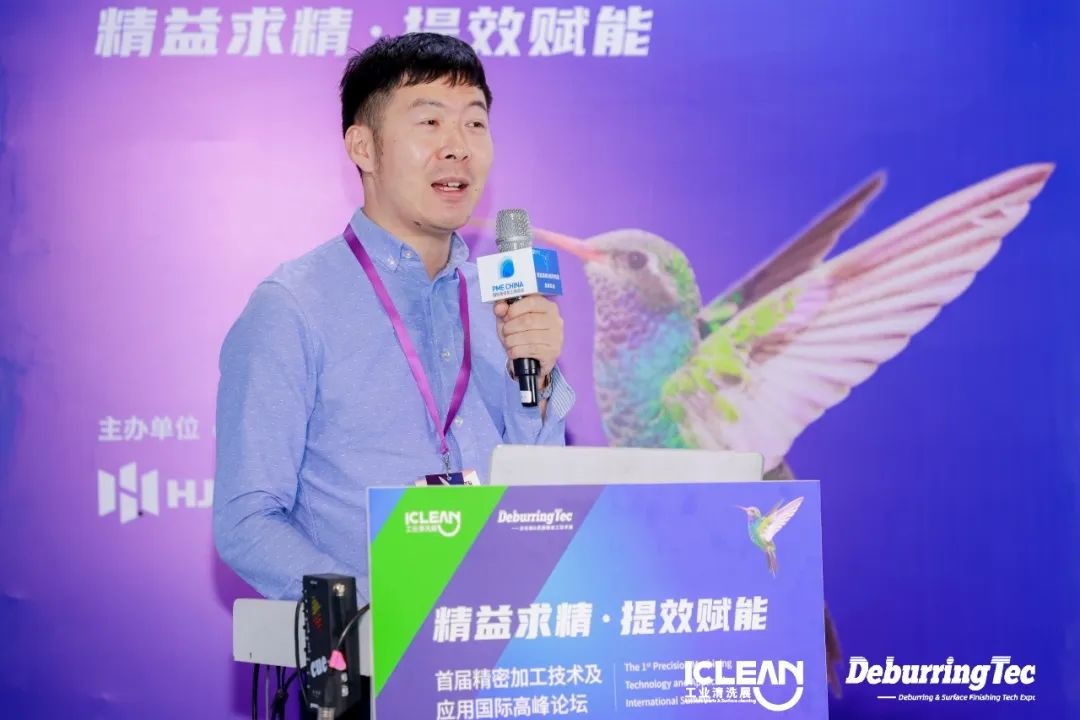
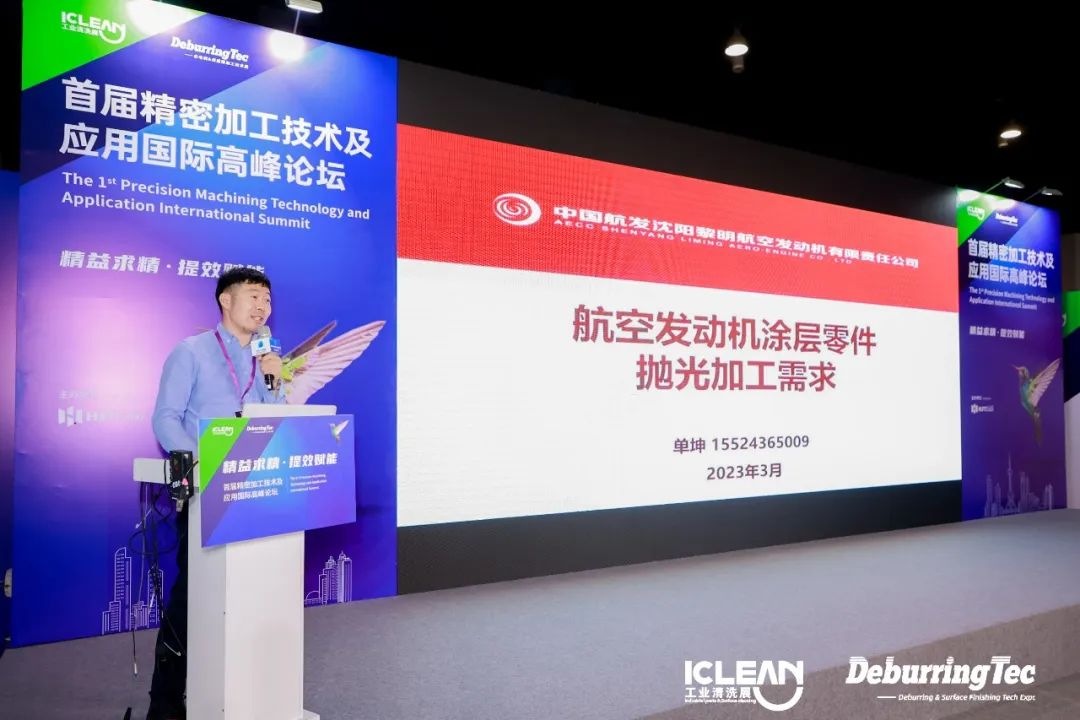
Shan Kun, senior engineer of AVIC Shenyang Liming Aero Engine Corporation Ltd., delivered a special speech on “Requirements for Polishing and Processing of Coated Parts of Aero Engines”
Engineer Shan introduced the discussion from three aspects: the significance of aero-engine coating polishing, the polishing requirements and expectations of coated parts. He introduced the characteristics of aero-engines and technology development trends, high-performance manufacturing requirements for turbine blades, high-performance manufacturing requirements for heat shields, and coating preparation methods. Mechanized polishing of body coatings and complex curved surface coatings; according to the characteristics of small batches and multiple varieties of aero-engines, general polishing equipment and tooling fixtures have been developed, which can realize rapid processing of various similar parts; strive to establish the service performance and polishing of final parts The relationship between processing parameters.


Professor Yang Shengqiang from Taiyuan University of Technology gave a special speech on “Development and Practice of New Process of Shape-property Collaborative Polishing for High-performance Parts Rolling Finishing”
Professor Yang described four aspects: the outline of barrel grinding technology, the stable industry-university-research cooperation, the practice of high-performance parts polishing, and the prospect of shape-property collaborative polishing.
In-depth analysis of the characteristics of the barrel finishing process and the processing purpose can improve the assembly process of the parts and realize the process of the parts assembly process; make the parts with the assembly relationship have better compatibility, repeatability and transferability, effectively Shorten the initial wear time after assembly of the whole machine; improve the service life of the parts themselves and the whole machine; improve the bonding force between the coating and the substrate to meet the special requirements for appearance. Then Professor Yang introduced the application of the new technology in practice, and looked forward to the future shape-property collaborative polishing, and came to the conclusion that the research and development of the technology is in line with the national strategy, serves the national defense construction, and meets the needs of the military and civilians.
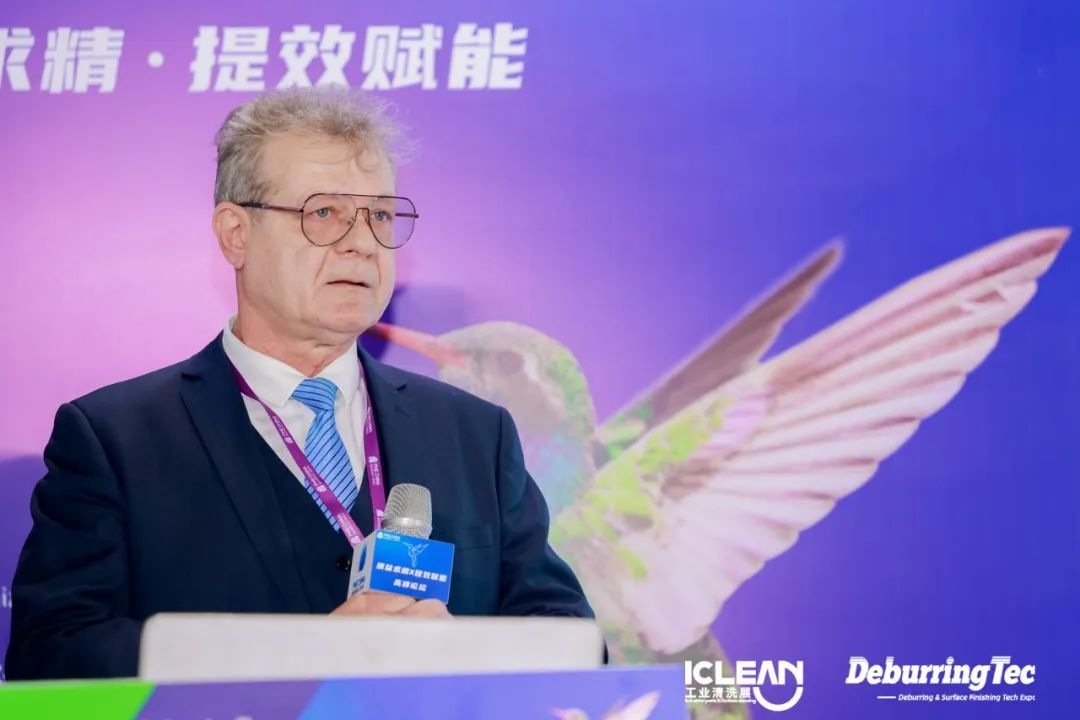
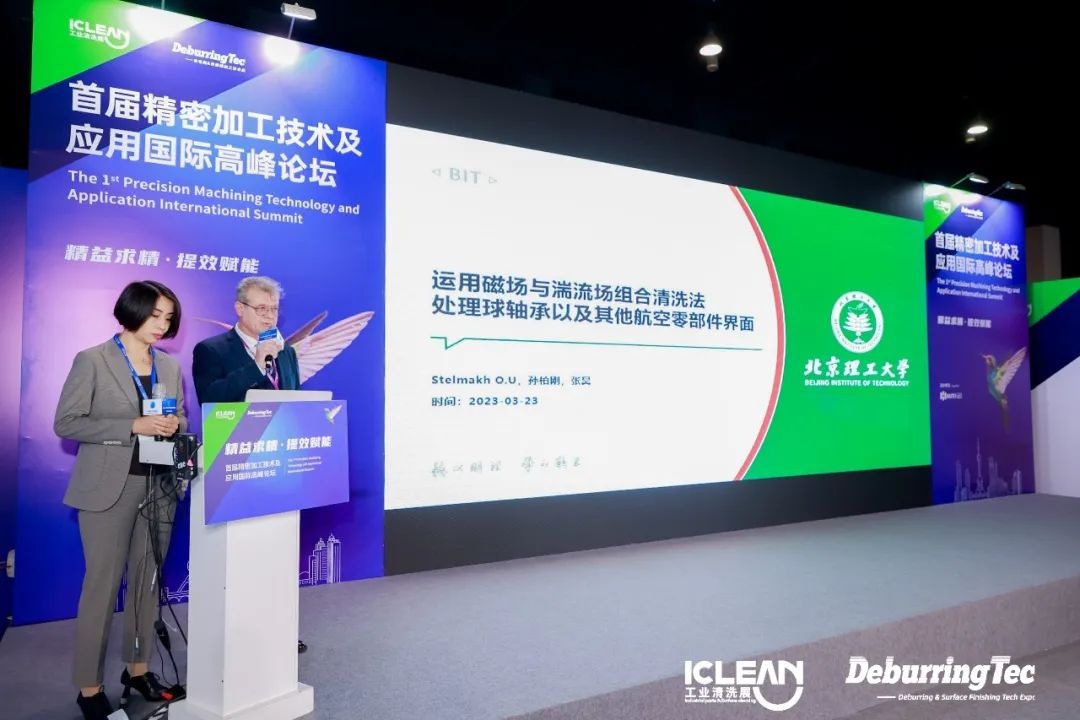
Distinguished Professor of Beijing Institute of Technology Alexander Sjerimach gave a special speech on “Using the combined cleaning method of magnetic field and turbulent field to treat the interface of ball bearings and other aviation parts”
Professor Alexander Sjerrymacher outlined the current status of the industry and said that friction, wear, and pollution hinder the development of aerospace. Non-separable ball bearings are probably the most common mass-produced friction components. They are characterized by a low coefficient of friction and a long service life. At the same time, he also introduced the non-separable aviation ball bearing cleaning station and its quality control system and other aviation precision parts cleaning stations, and introduced the team and other research directions. He let everyone understand the effect of different cleaning methods on the interface of ball bearings and other aviation parts through video presentations.
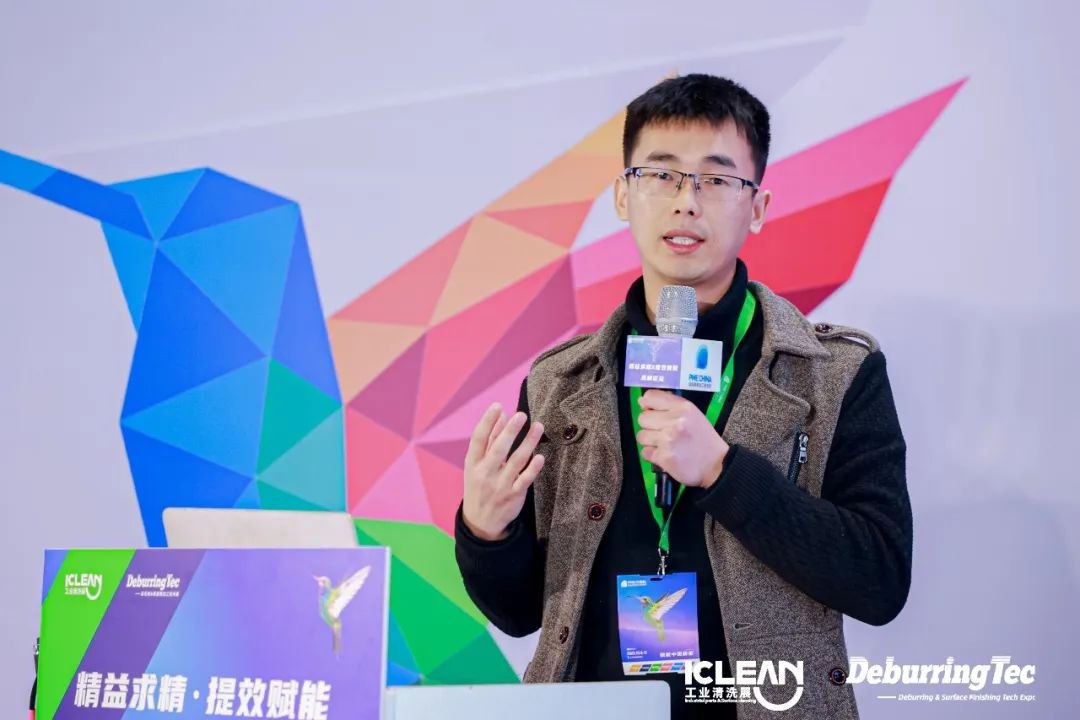
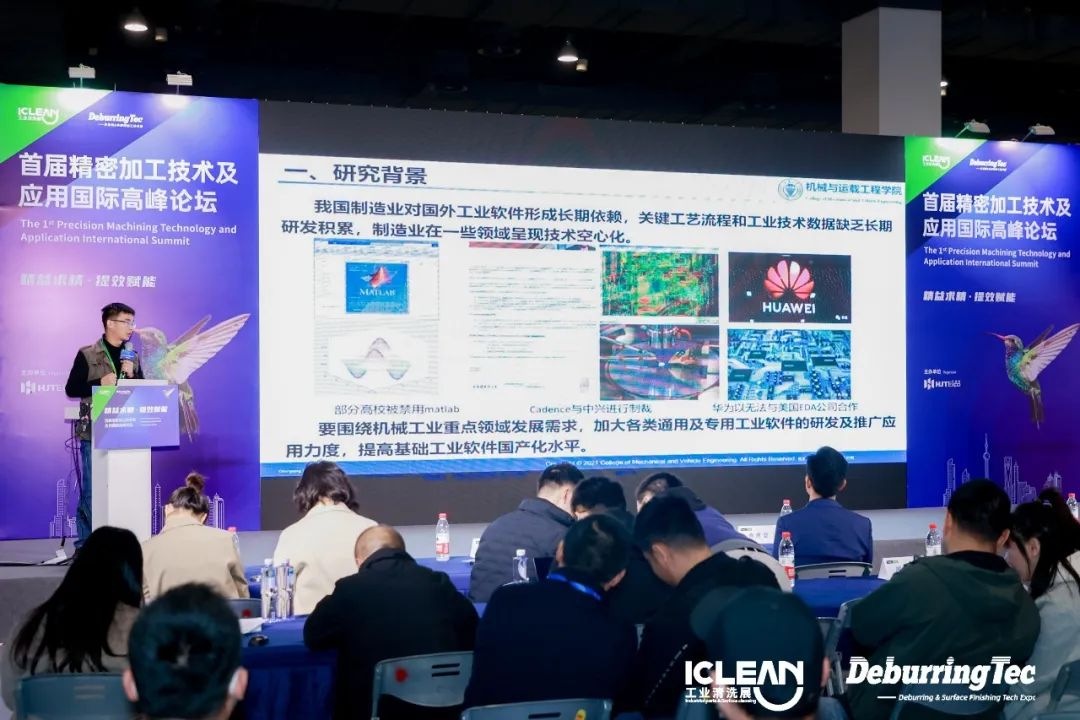
Liu Gang from the College of Mechanical and Vehicle Engineering of Chongqing University gave a special speech on “Intelligent Optimization Method and Software Development of Surface Grinding Parameters with High Service Performance”
Liu Gang first analyzed the background and significance of the research, and at the same time mentioned the main problems facing the development of related software in my country’s manufacturing industry: weak foundation, difficult application, shortage of talents, and insufficient innovation. Then he introduced the software platform and overall framework, software algorithms and research. The necessity of industrial software research is emphasized, and the processing intelligent control software is developed. The surface roughness prediction algorithm for abrasive belt grinding, the material removal rate prediction algorithm and the intelligent optimization method of processing parameters based on multi-objective optimization are studied to provide guidance for actual processing. In addition, the prediction of service performance such as fatigue life and residual stress has been studied.
Aiming at the defects on the surface of abrasive belt grinding, a defect identification and quantitative characterization method based on deep learning is proposed, and an in-depth analysis is carried out.
The theme of the afternoon forum is: Innovation and Development of Deburring & Surface Finishing Technology in Vertical Application
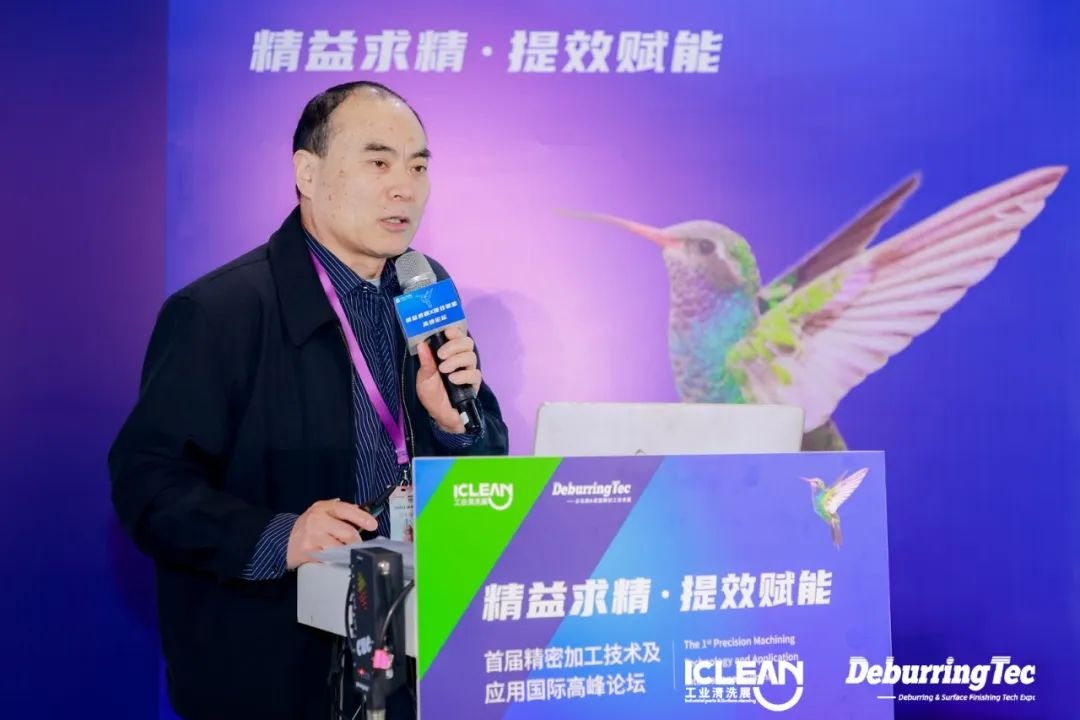
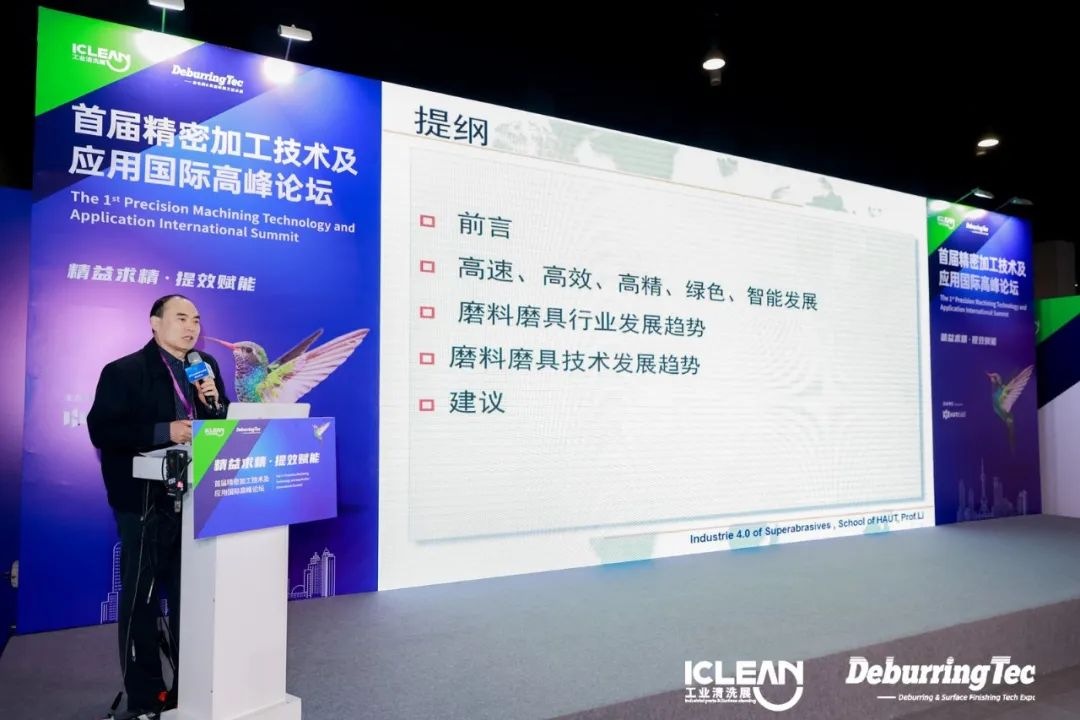
Li Zhengxin, deputy dean of the School of Materials of Henan University of Technology, delivered a special speech on “Development Status and Trends of Abrasives and Abrasives”
Professor Li analyzed the aspects of high-speed, high-efficiency, high-precision, green, and intelligent development, and then talked about the development trend of the abrasives industry and the development trend of abrasives technology. Professor Li said that innovation-driven, transformation and upgrading, and high-quality development are the industry’s development guidelines. The future development trend of abrasives and abrasives technology is reflected in bond research, molding technology, abrasive structure research, fourth-phase research, superabrasive research, superabrasive research, Hard abrasive and bonding agent interface, holding force and cutting edge height, etc. It is suggested that enterprises should transform and upgrade, and pay attention to the development mode of specialized, refined, special and new products; research on cutting, grinding and polishing technologies for difficult-to-process materials such as silicon, titanium alloys, and composite materials; from low-end to high-end, such as zirconium corundum, single crystal corundum, and ceramic corundum Direction development; provide solutions, change from manufacturing to service.
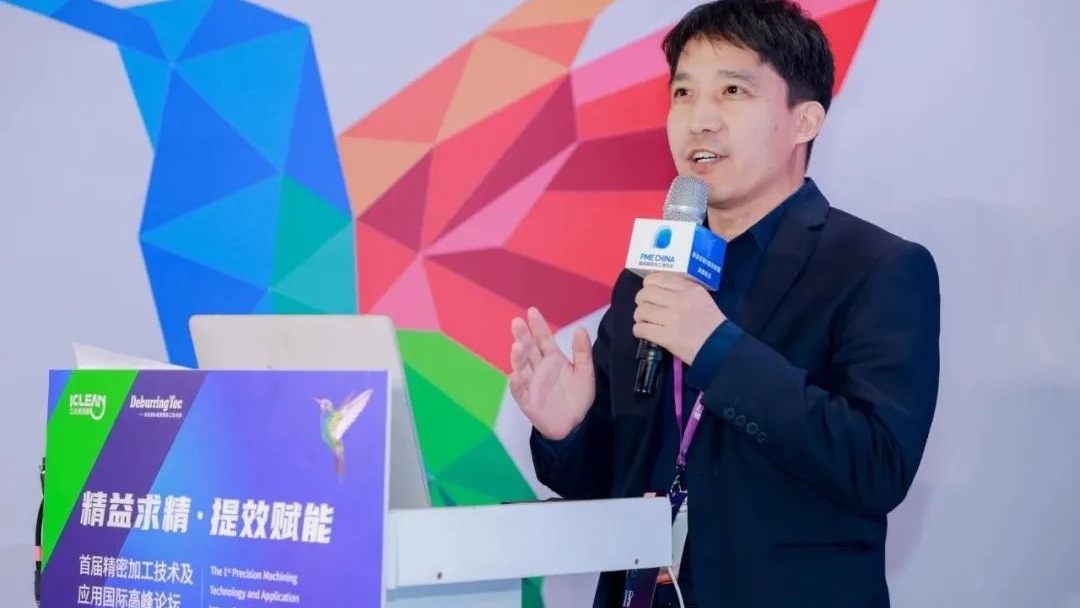

Zhang Zhiyu, a researcher of Changchun Institute of Optics, Fine Mechanics and Physics, Chinese Academy of Sciences, delivered a keynote speech on Ultra-precision Machining and Testing Technology of Optical Components
Zhang Zhiyu discussed the research background of ultra-precision optical components, introduced the ultra-precision machining method and technology of the mirror, and the ultra-precision detection method and practice of the mirror. The preparation process of SiC ceramics, abrasive water jet dressing of metal bonded grinding wheel, and three generations of polishing technology, including the characteristics of stress disk polishing, magnetorheological polishing, ion beam polishing and plasma polishing, are introduced in detail. Interferometric detection based on computational holographic elements is also presented.
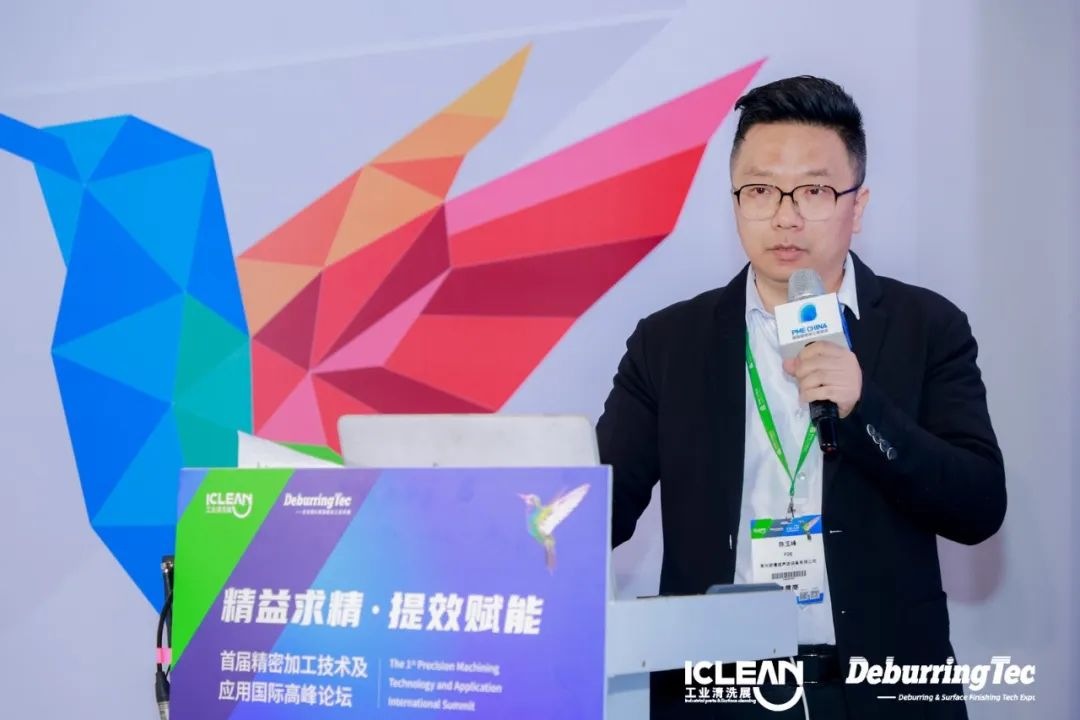
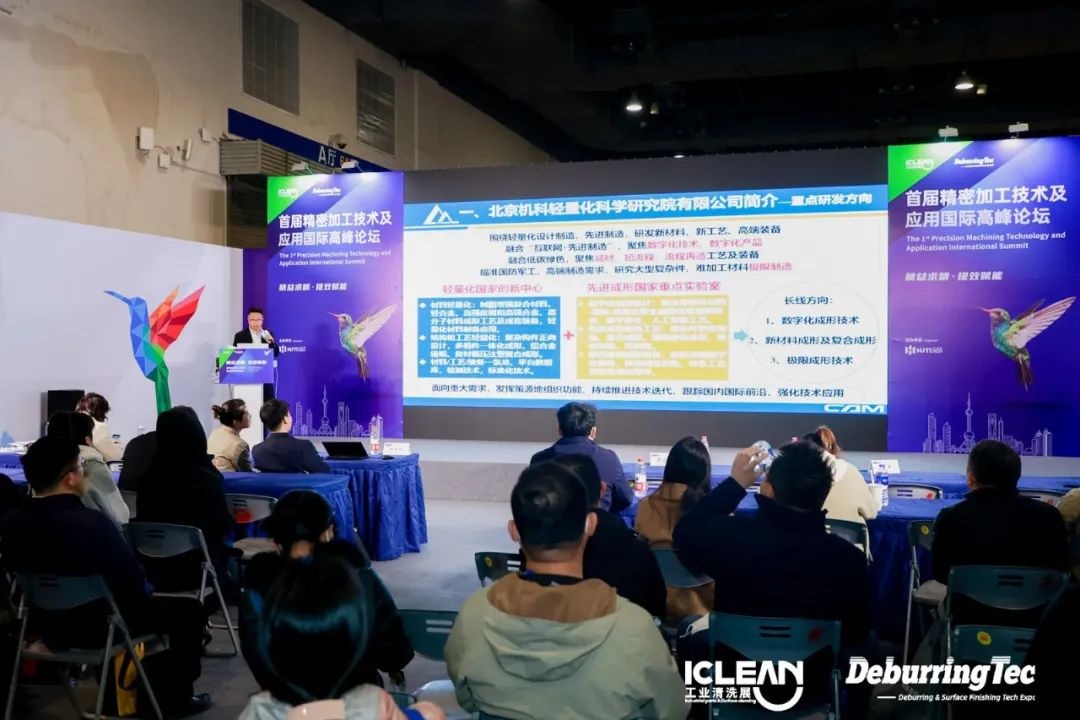
Chen Yufeng, director of the Joint Research and Development Center of Beijing Lightweight Research Institute, China Machinery General Institute, delivered a keynote speech on the overall solution of intelligent manufacturing of blade cell shell and the application of high-energy deburring Technology
Director Chen talked about the intelligent manufacturing solution for the new energy vehicle blade cell shell. He said that power battery shell materials are generally divided into aluminum shell and steel shell. Aluminum has the characteristics of easy processing and forming, high temperature corrosion resistance, good heat transfer and electrical conductivity. The aluminum power battery shell of aluminum alloy can be stretched at one time. take shape. Then, the cleaning and deburring equipment for the battery case and cover plate assembly and the principle of high-energy wave deburring technology were introduced in detail, and the effect of high-energy wave removal of laser cutting spatter before and after treatment was compared through a case.
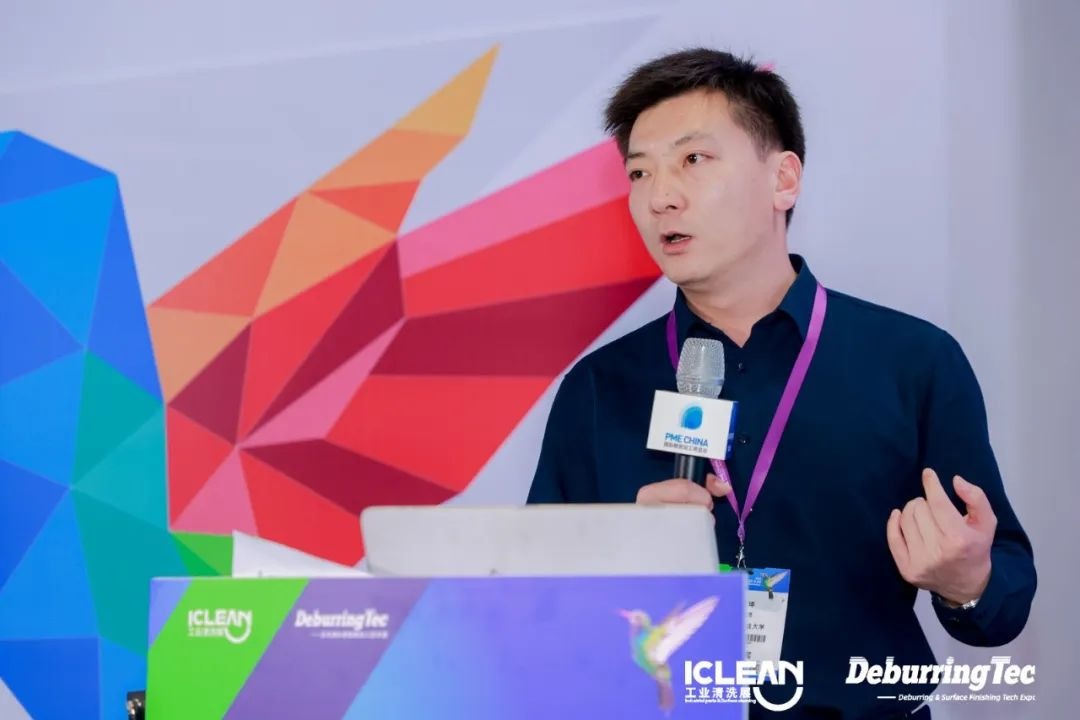
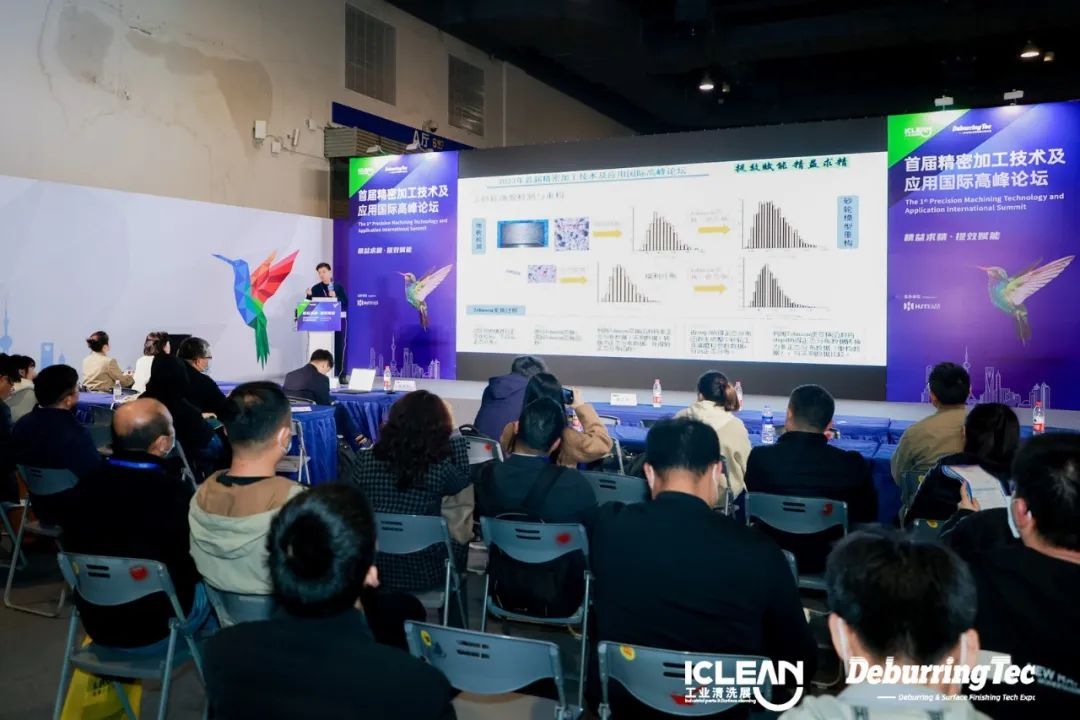
Ren Kun, a lecturer of the College of Mechanical Engineering, Suzhou University of Science and Technology, gave a special speech on “Application and Equipment of Ultrasonic Precision Machining Technology”
Teacher Ren said that the ultrasonic vibration grinding device integrates traditional grinding and ultrasonic vibration precision machining. It has the advantages of small cutting force, low cutting heat, low cutting temperature, slow tool wear, extended tool life, improved machined surface quality, small residual stress, and small subsurface damage. Then the working principle and parameters of the ultrasonic vibration grinding device were introduced, and finally the experimental research concluded that: the theoretical model of the uniform distribution of abrasive grain cutting thickness was established and the surface of the grinding wheel was reconstructed; the effect of grinding amount, ultrasonic vibration parameters on the face grinding force and The influence law of surface roughness; the influence law of CG and UAG grinding dosage and ultrasonic vibration parameters on subsurface damage.
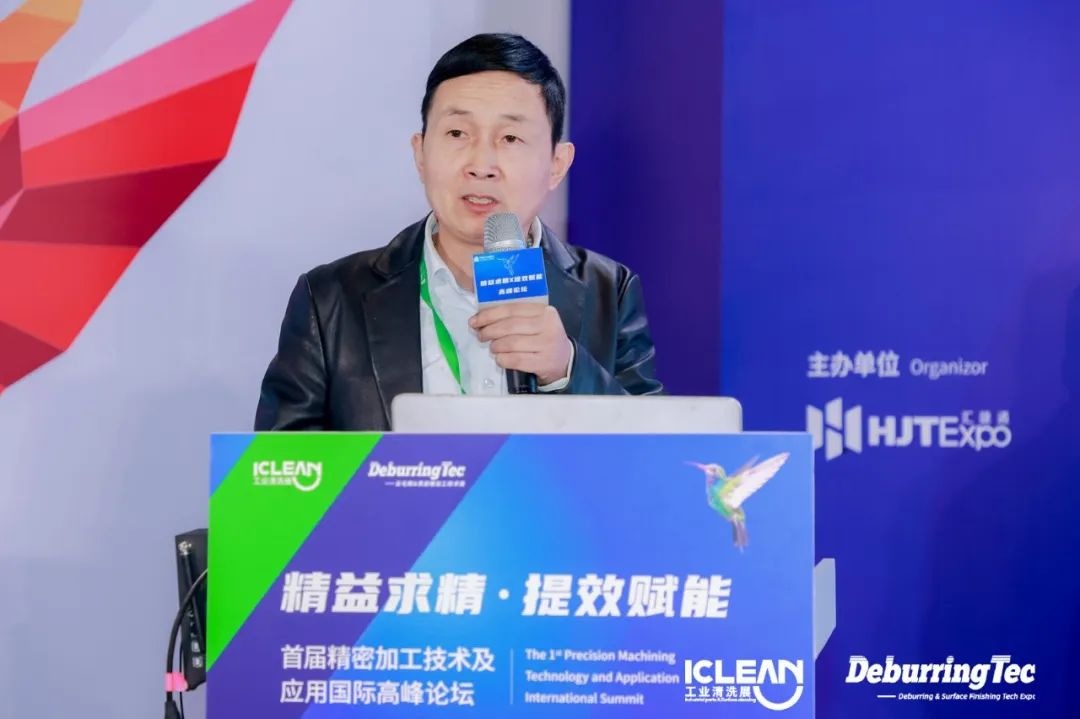
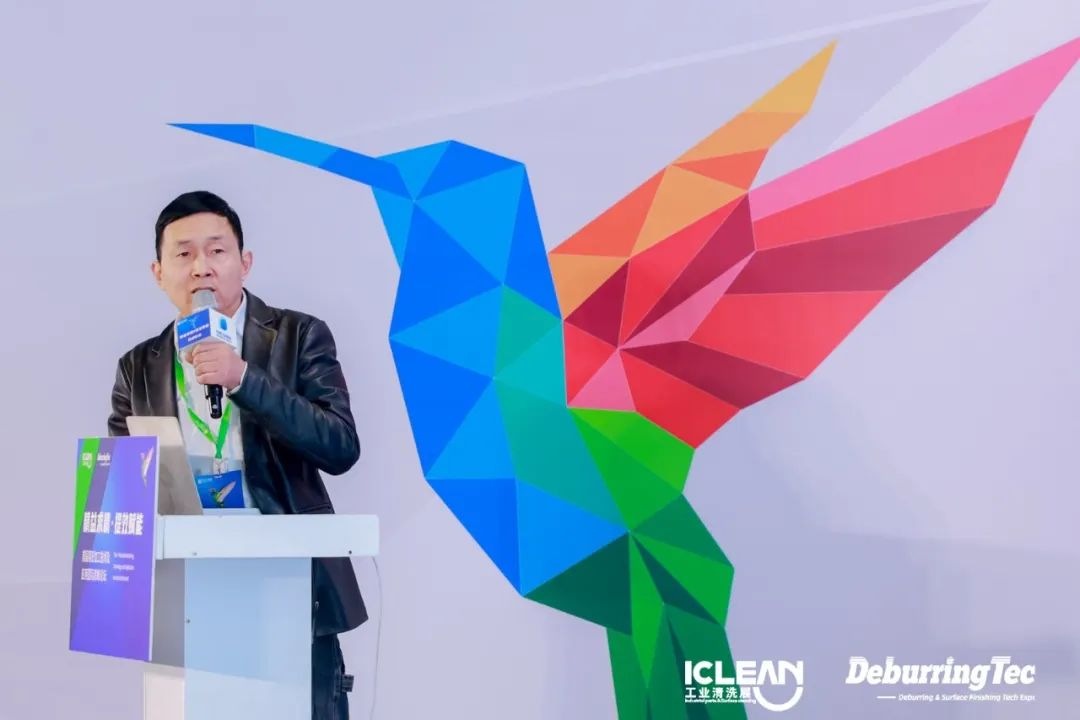
Gu Qingyun, general manager of Wanchuang (Suzhou) Intelligent Equipment Co., Ltd., gave a special speech on “One-stop Solution for Polishing and Grinding Process of Metal Cutting Parts”
Mr. Gu briefly analyzed the burrs, cleanliness, and rust problems of fine blanking parts, the deburring and rounding of fine blanking parts, cleaning and drying, and antirust technology, and the configuration of the deburring cleaning and drying antirust production line and the deburring cleaning and drying The dry anti-rust process standard is explained, and then the actual application case of deburring, cleaning, drying and anti-rust production is shown through the video, and the actual production of the deburring, cleaning and drying production line is demonstrated.
At 16:00, the forum activities ended successfully.
It is impossible to make new breakthroughs by traditional thinking and waiting in place. Nowadays, looking at trends, finding models, discussing directions, and listening to speeches are the general trend of the industry. This forum focused on the innovation and development of cutting-edge precision machining technology and its vertical application, which is of great significance to the development and advancement of global surface precision machining technology. Participants expressed that they have gained a lot, let us look forward to the next precision Come to the International Summit Forum on Processing Technology and Application!